What is Lean Six Sigma in Mississippi?
Contact Us
Why should you choose Six Sigma?
Motorola was the first company to incorporate Six Sigma in 1987. Following that, the quality control methodology’s development curve has been fascinating. Its development was slow at first, but it eventually gained popularity as a result of its positive results. As Jack Welch, then-CEO of General Electric, and Larry Bossidy, then-CEO of AlliedSignal, accepted Six Sigma in the mid-1990s, the technique’s early development potential was recognized. Many companies all over the world have adopted and reaped the advantages of this practice since then.
Six Sigma was once considered a “management fad” before becoming a quality management standard! Incredibly enough, Six Sigma has saved Fortune 500 companies millions and produced millions of dollars in projected earnings. As a result, it has shown that it is more than a fad in management.
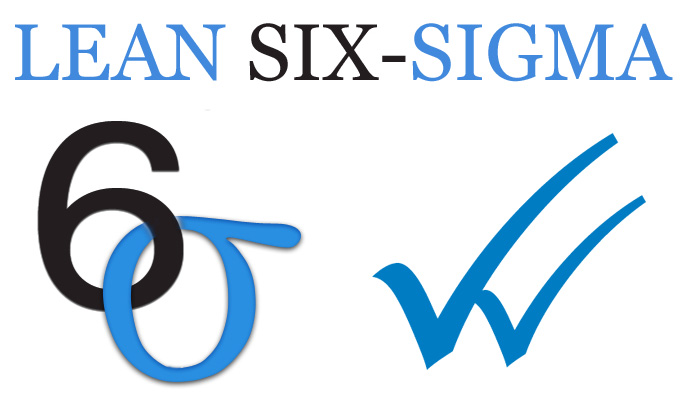
The Advantages of Using Six Sigma
When employed with accuracy and discipline, the Six Sigma methodology has many operational advantages. It improves consumer satisfaction and retention when any long-term focused enterprise aims to keep its current customers. Clients would stay faithful to your brand when you can keep them happy rather than switching to a different supplier or product offering. Do you have any concerns with customers who are dissatisfied with your service offerings? Many businesses may be unaware of this reality, and they may be planning market growth without understanding their consumer satisfaction ratings.
When you use Lean Six Sigma Experts of Mississippi’s approach, you exclude the risk of unhappy clients. We conduct a consumer dipstick test and help understand the critical aspects of your service or product that are needed for customer satisfaction and to effectively improve the consumer experience. When creating a business growth plan, we make sure you have all of the necessary components to intrigue buyer curiosity and inspire you to expand your client base.
In today’s retail environment, a mix of market expertise, efficiency, cutting-edge technology, and strict quality control is needed. Do you want your company to be recognized as a leader in the industry? Is one of the primary market goals to gain a strategic advantage over your competitors? To maximize the efficiency of available capital, Six Sigma methodologies are best used.
Frequently Asked Questions
Today's world is on the brink of advancement. If there is a distinction, it is because the rate of transition accelerates with each passing year. In an enterprise, management's role is to create systems, as well as value-adding manufacturing and delivery systems for consumers and company owners; this is a continuous process. Competitors must adapt to retain customers. Customers receive goods and services in different ways as a result of innovations. Customer tastes are changing at a breakneck rate. What appeals to you now may become a must tomorrow. The "change necessity" is something that all organizations need to be aware of. Companies have to adapt or may face extinction if they want to advocate change in the industry. Lean Six Sigma Experts of Mississippi are on board with the shift. We support the continual development of methodologies in terms of consistency and timeliness. Management must still be looking for innovative ways to improve product and service offerings. Rather than a collection of services, operational transformation becomes a way of life. Lean Six Sigma is a form as well as a collection of methodologies. When it comes to encouraging change in their sectors, managers should look to these as a resource. Management and development branches employ Black Belts and Master Black Belts. This indicates that Six Sigma is on the right track and is assisting in the achievement of organizational objectives. The performance will be determined by which Lean Six Sigma partner a company chooses, as it is when selecting every other partner, manufacturer, or supplier. It seems only appropriate to apply expertise when creating a few frequently asked questions when assessing prospective partners. Here are some of the most commonly asked questions, along with some tips about the types of responses to expect: Your Lean Six Sigma partner must, at the very least, have a Six Sigma delivery and instruction model in place, as well as an accomplished Master Black Belt on hand to assist with project practice and mentoring. The Master Black Belt should have real-world knowledge and be familiar with the company's culture, environment, and clients. During their preparation, candidates can create tools and adapt them to real-world scenarios. When managing courses across assignments, it's common to provide project impact indicators so that students can translate their preparation into project results. To ensure the services are completed on budget and with good performance, which involves measuring dollars realized, cycle times, and plan slippage, as well as toll-gates. The Master Black Belt will also generate coaching reports to consider and resolve personnel and operational project issues. It's critical to comprehend an organization's ability to implement Lean Six Sigma, when making a transition. Your implementation partner can lay the foundation for continuous deployment by outlining tasks for a readiness analysis. This involves assessing ongoing efforts in action or process, as well as evaluating potential progress plans and possible programs. A planning assessment should include a summary of the void study's for potential development, as well as an analysis of consumer and market survey results. Both of these elements can contribute to the identification of potential development risks, which can then be resolved. Six Sigma analyzes scenarios and measures outcomes using mathematical methods. Six Sigma calculations are based on inferential statistics and probability hypotheses. However, six sigma is more than just a collection of numbers. It's a set of techniques for defining what customers want and aligning the organization's tools, like measuring systems, to deliver their requirements. Six Sigma decreases the number of unexpected events (variation) and increases objectivity in assessing results (what “good” means), especially in terms of customer execution. To be a Six Sigma specialist, you must have a strong desire to offer excellent customer service, be able to challenge the status quo daily, and provide a basic understanding of statistics. Why Six Sigma?
How does Lean Six Sigma work?
How do you handle managing classes through their projects?
How can you incorporate your program with the work that our company is already doing?
Six Sigma is about statistics, do I need to learn statistics?

What is the difference between Six Sigma and Lean?
The Lean method is used to eliminate waste in a systematic manner (called Muda in Japanese). There are seven types of waste in sports, according to Taiichi Ohno (TPS fame). To deliver service to consumers, it is critical to recognize and eradicate waste. To improve company operations and efficiency, both the Lean and Six Sigma methodologies are used. Lean is associated with systems, flow optimization, and performance gains. Six Sigma is concerned with increasing productivity, performance, and effectiveness.
There are so many areas or regions where we offer these services with most of them being cities.
However, if you need any of these services, you need to contact us. The list below comprises the areas where we offer these services.